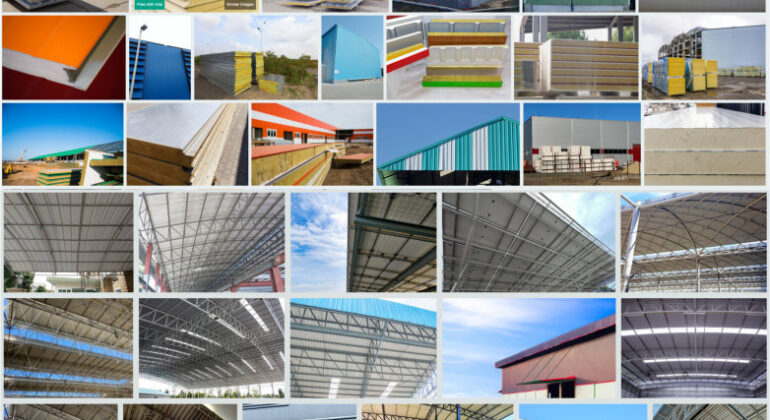
How to build Cold Storage Buildings with Sandwich Panels
Cold storage buildings play a critical role in industries that rely on temperature-controlled environments to store perishable goods such as food, pharmaceuticals, and chemicals. Ensuring these storage facilities are built efficiently and with high-quality materials is key to maintaining optimal temperature control and long-term durability.
One of the most effective ways to construct cold storage buildings is by using sandwich panels in Pakistan, which offer superior insulation, energy efficiency, and cost-effectiveness. In this comprehensive guide, we will walk you through the process of designing and building a cold storage facility using sandwich panels, highlighting the benefits and technical considerations.
What Are Sandwich Panels?
Sandwich panels are a type of composite material made up of two outer metal sheets (often steel) with an insulating core in between. The core can be made of various insulating materials, including:
-
Polyurethane (PUR)
-
Polystyrene (EPS)
-
Mineral wool
This combination of materials offers exceptional thermal insulation properties, which is crucial for cold storage buildings where temperature control is essential.
Why Use Sandwich Panels for Cold Storage Buildings?
1. Superior Insulation Properties Sandwich panels provide excellent thermal insulation, which is key to maintaining a stable internal temperature in cold storage units. The insulating core helps prevent the escape of cold air and minimizes heat transfer from the external environment, which reduces energy consumption and helps maintain the desired temperature.
2. Energy Efficiency Given the high energy demands of cold storage buildings, the energy efficiency provided by sandwich panels is invaluable. These panels help minimize the costs associated with heating and cooling, leading to lower energy bills over time.
3. Durability and Strength The outer metal layers of sandwich panels protect the insulating core, making them resistant to physical damage, moisture, and corrosion. This makes them ideal for harsh environments where cold storage units are exposed to constant temperature fluctuations.
4. Quick Construction The pre-fabricated nature of sandwich panels allows for faster construction times. The panels are easy to handle and install, reducing labor costs and time spent on-site.
5. Flexibility in Design Sandwich panels come in various thicknesses, finishes, and colors, allowing for customized designs that meet the specific requirements of the cold storage building, including size, load-bearing capacity, and aesthetic considerations.
Steps to Build a Cold Storage Building with Sandwich Panels
Building a cold storage facility involves several steps, from planning and design to installation. Below is a step-by-step guide to help you understand the process.
Step 1: Site Selection and Planning
Before you begin construction, selecting the right site is crucial. Factors such as the proximity to your target market, local climate conditions, and accessibility must be considered. The site should be flat and stable, with sufficient space to accommodate the size of the cold storage building.
Key Considerations:
-
Local zoning regulations
-
Drainage and flood protection
-
Soil testing for foundation stability
-
Proximity to transportation networks
Step 2: Design and Engineering
Once the site is selected, the design phase begins. A team of architects and engineers will work together to ensure the building meets all functional requirements. The design should consider factors like temperature control, airflow, layout, and structural integrity.
Key Design Aspects:
-
Temperature Requirements: Decide on the specific temperature range for your cold storage (e.g., deep freezing, refrigerated, etc.).
-
Ventilation and Airflow: Proper airflow is essential to ensure uniform temperature distribution inside the storage unit.
-
Shelving and Storage Layout: The interior layout should be optimized for efficient storage and retrieval of goods.
During this phase, it’s essential to choose the appropriate thickness and type of sandwich panels based on the required insulation performance and the external environmental conditions.
Step 3: Foundation and Structural Framework
The foundation is the first structural element that needs to be laid down. It should be designed to support the weight of the building and the storage equipment inside. Concrete is often used for the foundation due to its strength and stability.
Once the foundation is complete, the structural framework of the building is erected. This framework is typically made of steel, which provides strength and flexibility, and is designed to support the sandwich panels during installation.
Key Considerations:
-
Steel columns, beams, and trusses
-
Foundation depth and type based on the building’s load-bearing capacity
-
Structural connections for sandwich panels
Step 4: Installation of Sandwich Panels
Once the framework is in place, the sandwich panels are installed as the building’s walls and roof. The panels are usually installed using mechanical fasteners and sealants to ensure they fit tightly and securely.
Installation Process:
-
Wall Panels: Sandwich panels are mounted onto the steel framework to form the walls of the cold storage unit. The panels are fixed with bolts and seals to prevent air leakage.
-
Roof Panels: Similar to the walls, the roof is made using insulated sandwich panels. The panels are installed in overlapping sections to ensure a weather-tight seal.
-
Insulation Integrity: Ensure that the seams and joints between panels are properly sealed to maintain the thermal efficiency of the building.
Step 5: Temperature Control Systems and Electrical Installations
Cold storage buildings require specialized refrigeration systems to maintain the desired temperature. These systems include compressors, evaporators, and condensers that work together to cool the interior.
Key Considerations for Refrigeration:
-
Type of refrigeration system (e.g., centralized or decentralized)
-
Capacity based on the size of the cold storage unit
-
Installation of temperature monitoring and control systems
In addition to the refrigeration system, electrical systems such as lighting, alarms, and automated doors need to be installed.
Step 6: Final Inspections and Testing
Once construction is complete, the cold storage facility should undergo thorough inspections to ensure that it meets all building codes, safety standards, and operational requirements.
Testing:
-
Thermal Performance: Test the temperature consistency throughout the cold storage facility to ensure it meets the required standards.
-
Refrigeration Efficiency: Check the refrigeration system’s performance to ensure it operates efficiently and maintains the desired temperature.
-
Electrical and Safety Systems: Verify the functionality of alarms, emergency lighting, and backup power systems.
Step 7: Ongoing Maintenance
After construction, regular maintenance is essential to keep the cold storage building in optimal condition. This includes checking the refrigeration system, replacing damaged panels, and ensuring the integrity of the seals and insulation.
Building a cold storage facility using sandwich panels is an efficient, cost-effective, and energy-saving method that ensures the longevity and reliability of your storage solutions. By following this step-by-step guide, businesses can create high-quality cold storage buildings that are well-insulated, durable, and capable of maintaining strict temperature control.
Whether you are storing food, pharmaceuticals, or other perishable goods, sandwich panels are an excellent choice for constructing cold storage buildings that will help you keep your products safe and your energy costs low.
If you’re considering building a cold storage facility and want to learn more about how sandwich panels can enhance your project, [Your Company Name] offers comprehensive design, manufacturing, and installation services. Get in touch today for expert guidance on your next cold storage building project.